潍坊环评_固废专题
时间:2020-06-25
潍坊环评_固废专题
表1 项目产品一览表
本项目主体工程、公用工程、环保工程实际情况和原环评对比,见表2。
表2 项目工程内容
本项目原辅材料及用量
表3本项目原辅材料及用量
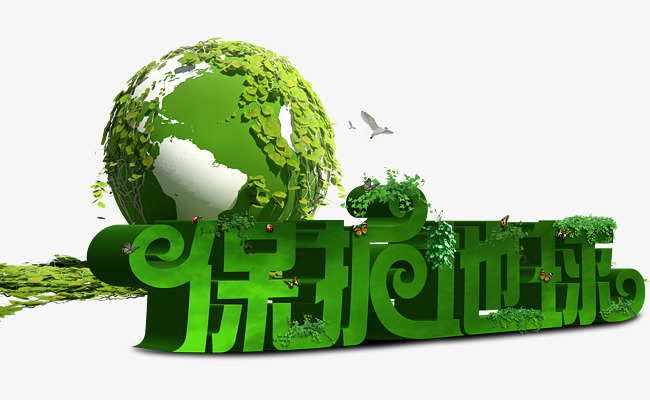
挤压生产工艺介绍
原料准备
铝棒加热:铝棒运至挤压车间,经过热剪炉加热、裁切成适合后续设备加工的长度,热剪炉以市政天然气为燃料,采取循环热风加热方式,保证加热温度在480~560℃,达到加工温度后方可进行挤压操作。铝棒加热炉每天运行时间约为18h(年运行时间为5400h)。
此过程产生二氧化硫、氮氧化物和烟尘等。
模具预热:根据生产计划选用相应规格模具,送入模具加热炉加热,采取电磁感应加热方式,加热温度在440~460℃,根据机台规格控制模具保温时间,一般保温时间大于2~4小时,但不超过12小时,满足装模温度后方可装模,装模速度应快,根据机台规格应控制在2~5分钟。挤压机模具应定期进行维护修理,修模以人工修整+氮气强化为主。
盛锭筒(挤压筒)预热:盛锭筒应保持清洁干净,并经常清缸,首次开机时采取电加热方式进行预热,加热温度控制在380~400℃,满足加工温度后方可投入生产,正常生产后盛锭筒依靠铸锭自身的余温维持筒内温度,不再需要额外加热措施。
挤压成型
根据生产计划组织挤压生产,首先检查盛锭筒温度、模具温度、铸锭温度是否达到工艺加工要求,全部达到要求时方能装模挤压。根据铸锭、所加工挤压材形状、尺寸、模具工作状态等因素,合理控制挤压速度,确保产出的挤压材光滑平直。采取首件检查方式,检查挤压出的第一支基材尺寸、表面是否符合技术工艺要求,然后将料头切割300mm作为修模依据,另切200mm取样进行外观、尺寸、形状检查,符合技术条件后方可继续生产,否则进行换模、修模处理。
此过程产生下角料、废液压油、废机油等。
风冷淬火
连续产出的挤压型材应合理配制尺寸长度,在适当位置裁断,并通过风机强制冷却淬火,然后传送至冷床上继续利用风机冷却,冷却至50℃以下后,方可进行拉伸矫直处理。
拉伸矫直
冷却后的挤压材经输送带送至拉伸矫直机,首先检查长度、断面尺寸,确保夹头位置和延伸率,其中延伸率一般控制在0.05-2%左右,然后进行拉伸矫直整理,矫直后检查铝材无波浪、弯曲、扭拧等,同时避免出现收口、张开、尺寸负差等现象。
锯切
矫直后的挤压材送至锯切区,首先检查其截面质量、表面质量是否存在缺陷,然后将不合格段切除,再定尺锯切。按照技术工艺要求,控制挤压材的长度公差、切斜度偏差等,防止出现负偏差,完成锯切后修理断面,做到无变形、无毛刺、无油污且整齐美观,然后将合格挤压基材整齐摆放入料筐内,按照同批订单、同种色样、同一型号堆叠,并过磅称重,作好记录后转入下道工序。
锯切过程产生的铝屑。
时效
加工好的挤压基材送入时效炉内消除材料的残余应力,时效炉以市政天然气为燃料,采取热风循环加热方式,温度控制在195~205℃之间,保温时间根据基材形状、壁厚进行控制,测量铝材硬度,达到技术要求后送入检验区检验。时效炉每天运行时间约为12h(年运行时间为3600h)。
此过程产生二氧化硫、氮氧化物和烟尘等。
检验入库
时效后的基材送入检验区,按挤压基材检验规程分别对每料筐基材进行表面质量和机械性能检验,检验合格后按照同批订单、同种色样、同一型号的原则转至指定位置存放,以备后续加工使用。
项目产品方案及原辅材料
项目产品方案同原环评比较见表1表1 项目产品一览表
产品类别 | 原环评 |
实产能力 (吨/年) |
||
主要生产工艺 | 生产车间 |
原环评产量 (吨/年) |
||
铝棒 | 铝锭及辅料镁、硅等 | 熔铸车间 | 5120 | 0 |
基材 | 变形铝及铝合金圆铸锭一挤压一时效 |
挤压车间 |
未分析 | 33000 |
阳极氧化型材 | 基材一阳极氧化-电解着色或不着色-封孔 |
氧化车间 |
20000 | 6000 |
电泳涂漆型材 | 基材一阳极氧化一电解着色一电泳—固化 |
电泳车间 |
10000 | 6000 |
粉末喷涂型材 | 基材一除油一钝化一烘干一喷粉—固化 |
喷涂车间 |
20000 | 5000 |
项目工程内容
工程内容本项目主体工程、公用工程、环保工程实际情况和原环评对比,见表2。
表2 项目工程内容
原环评 |
实际 情况 |
|||
序号 | 工程主要建设内容 | |||
1 | 主体工程 |
挤压车间 时效车间 |
建筑面积4493.98m2,用于铝棒挤压成型。16套挤压机,行车6台,时效炉2台。 | 建筑面积9792m2,用于铝棒挤压成型。8套挤压机,行车6台,时效炉2台。 |
2 | 喷涂车间 | 建筑面积1320m2,承担铝型材喷涂任务。2条喷涂线。 | 建筑面积2300m2,承担铝型材喷涂任务。1条喷涂线。 | |
3 | ||||
4 | 氧化车间 | 建筑面积2040m2,承担铝型材氧化任务。1条氧化生产线。 | 建筑面积1842m2,承担铝型材氧化任务。1条氧化生产线。 | |
5 | 电泳车间 | 无 | 电泳线1条,行车2台。 | |
6 | 包装车间 | 建筑面积1320m2,承担铝型材成品、半成品包装任务。 | 建筑面积2322m2,承担铝型材成品、半成品包装任务。 | |
7 | 熔铸车间 | 建筑面积876.8m2 | 无 | |
二 | 辅助工程 | |||
1 | 成品库 | 未建 | 建筑面积5040m2,承担铝型材基材、成品存放任务。存 | |
2 | 模具房 | 未建 | 模具房1处,存放模具。 | |
3 | 五金库 | 未建 | 五金库1处,存放原辅材料。 | |
4 | 宿舍楼、职工食堂 | 1座,建筑面积360m2 | 1座,建筑面积929.61m2 | |
三 | 公用工程 | |||
1 | 供电系统 | 由临朐供电局220kV弥南站35kV出线线路引入厂区变配电站降压至0.4kV后输送至各用电单元作为生产、生活电源 | 由临朐供电局220kV弥南站35kV出线线路引入厂区变配电站降压至0.4kV后输送至各用电单元作为生产、生活电源 | |
2 | 供水系统 | 取自临朐沂山自来水有限公司供水管网,临朐沂山自来水有限公司现每天供水能力8万吨/日,供水能力、供水水质、供水压力均能满足项目需要 | 取自临朐沂山自来水有限公司供水管网,临朐沂山自来水有限公司现每天供水能力8万吨/日,供水能力、供水水质、供水压力均能满足项目需要 | |
3 | 排水系统 | 排水系统实行雨污分流,雨水进入雨水管网 | 排水系统实行雨污分流,雨水进入雨水管网 | |
4 | 供气系统 | 由临朐港华燃气有限公司供给,厂区内建有调压站,同时在厂区内敷设燃气管道,输送至各个生产车间,以满足生产需要 | 由临朐港华燃气有限公司供给,厂区内建有调压站,同时在厂区内敷设燃气管道,输送至各个生产车间,以满足生产需要 | |
四 | 环保工程 | |||
1 | 废气治理系统 | 天然气燃烧产生的废气经集气罩收集后由20米排气筒P1排放,固化炉产生的固化废气经过活性炭吸附后通过20米烟囱排放 | 天然气燃烧产生的废气经集气罩收集后由20米排气筒P1排放,固化炉产生的固化废气经过活性炭吸附后通过18米烟囱排放 | |
2 | 污水处理系统 | 污水处理站1座 | 污水处理站1座 | |
3 | 危险废物暂存、贮运系统 | 危险废物库2座 | 危险废物库2座 |
表3本项目原辅材料及用量
序号 | 名称 | 年消耗量(t) | 厂内储存量(t) | 有效含量(%) |
1 | 铝棒 | 55000 | 800 | / |
2 | 硫酸 | 150 | 6 | 98 |
3 | 氢氧化钠 | 100 | 4 | 99 |
4 | 硫酸亚锡 | 37.5 | 1.5 | 90 |
5 | 钝化剂 | 30 | 0.9 | 90 |
6 | 喷涂粉末 | 450 | 18 | / |
7 | 隔热条 | 750 | 50 | / |
8 | 包装膜 | 125 | 5 | / |
9 | 包装纸 | 350 | 15 | / |
10 | 电泳漆 | 300 | 11 | / |
11 | 着色剂 | 35 | 1.5 | 90 |
项目固体废物统计
项目固体废物产生情况与本次评价实际调查项目固体废物产生情况对比见表4。固体废物来源 | 污染物名称 |
产生环节(t/a) |
实际运行产生量(t/a) | 固废性质 | 固体废物形态 | 危险类别 | 原环评量(t/a) | 处置方式 |
熔铸车间 | 熔铸铝灰 | 熔铸 | 0 | 一般固废 | 固态 | —— | 5020 | —— |
挤压车间 | 废液压油、废机油等 | 挤压成型 | 0.55 | 危险废物 | 液态 |
废矿物油 HW08 |
未分析 | 委托山东平福环境服务有限公司处置 |
下角料 | 挤压成型 | 5110 | 一般固废 | 固态 | —— | 未分析 | 外售处置 | |
铝屑 | 锯切 | 2200 | 一般固废 | —— | 未分析 | 外售处置 | ||
喷涂车间 | 回收塑粉 | 喷粉 | 1.25 | 一般固废 | —— | 未分析 | 回收用于生产 | |
废滤芯 | 过滤 | 0.5 | 危险废物 | 其他废物HW49 | 未分析 | 委托山东平福环境服务有限公司处置 | ||
废活性炭 | 吸附 | 0.6 | 危险废物 | 其他废物HW49 | 未分析 | |||
除油废槽渣 | 除油 | 0.88 | 危险废物 |
表面处理废物 HW07 |
80t |
|||
钝化废槽渣 | 钝化 | 0.65 | 危险废物 |
表面处理废物 HW17 |
||||
氧化车间 | 酸洗废槽渣 | 酸洗 | 0.35 | 危险废物 |
表面处理废物 HW17 |
|||
抛光废槽渣 | 抛光 | 0.38 | 危险废物 |
表面处理废物 HW17 |
||||
碱蚀废槽渣 | 碱蚀 | 0.6 | 危险废物 |
表面处理废物 HW17 |
||||
中和废槽渣 | 中和 | 0.88 | 危险废物 |
表面处理废物 HW17 |
||||
阳极氧化废槽渣 | 阳极氧化 | 0.9 | 危险废物 |
表面处理废物 HW17 |
||||
封孔废槽渣 | 封孔 | 0.13 | 危险废物 |
表面处理废物 HW17 |
||||
含镍废槽渣 | 着色 | 0.38 | 危险废物 |
表面处理废物 HW17 |
||||
电泳废槽渣 | 电泳 | 0.9 | 危险废物 |
表面处理废物 HW17 |
||||
废弃活性炭 | 固化 | 0.7 | 危险废物 | 其他废物HW49 | 未分析 | |||
废包装桶 | 配槽液 | 2.5 | 危险废物 | 其他废物HW49 | 未分析 | |||
污水处理 | 综合污泥 | 污水处理 | 6.25 | 危险废物 | 表面处理废物HW17 | 8.28 | ||
含铬污泥 | 污水处理 | 1.55 | 危险废物 | 危险废物(HW21 含铬废物) | 未分析 | |||
含镍污泥 | 污水处理 | 1.67 | 危险废物 | 危险废物 (HW17表面处理废物) | 未分析 | |||
生活垃圾 | 职工生活 | 36 | 一般固废 | —— | 36 | 由环卫部门定期清理 | ||
合计 | 7367.62 | 5244.8 |
项目原环评批复及验收要求落实情况
企业对环评验收整改措施和要求中落实情况见表5环评批复环保做事要求 | 实际环保措施情况 | 落实情况 |
严格遵守污染防治设施与主体工程同时设计、同时施工、同时投产的“三同时”原则。 | 严格执行 | 已落实 |
做好施工期间的水土保持工作,工程开挖应避开雨季;采取有效的措施抑制施工扬尘,运输车辆应采取防止物料洒落的措施;及时对场地进行硬化和绿化。施工期间噪声应达到《建筑施工场界环境噪声排放标准》(GB 12523-2011)的标准。 | 严格执行 | 已落实 |
项目建成后,铝材的氧化生产过程中自来水水洗槽液使用一定时间后排入厂区的废水处理池;电解着色槽、封孔槽槽液经处理后全部回用,不外排;表面酸洗脱脂槽、碱蚀槽、中和出光槽、阳极氧化槽的槽液在Al3+达到一定浓度时,槽液部分排排入厂区废水处理池。落实好环评中的提出的废水处理方案,确保污水处理设施稳定正常运行。生活废水净化粪池处理后与经处理后的工艺废水一起经污水管网进入临朐县污水处理厂进一步处理,废水排放应确定达到《污水排入城市地下水道标准》(GB/T 31926-2015)中的要求。 | 严格执行 | 已落实 |
采取合理布局,对挤压机、行车等设备应采取减振、吸声、隔声等措施,确保厂界噪声满足《工业企业厂界环境噪声排放标准》(GB12348-2008 中2类区标准要求。 |
1、在满足工艺设计的前提下,尽量选用低噪声设备,并将噪声较高的设备设在车间内远离项目厂界的位置; 2、在挤压机、风机等运转噪声较大的设备安装减振垫。 |
已落实 |
熔铸炉、铝棒加热炉和时效炉燃烧天然气所产生的废气由风机抽至配气筒后集中排放,排气筒高度为20米。废气排放采取切实有效的污染防治措施,确保达到山东省工业炉窑大气污染物排放标准》(DB37/2375-2013)中表2中二级标准的要求。 | 熔铸炉、铝棒加热炉和时效炉燃烧天然气所产生的废气由风机抽至配气筒后集中排放,排气筒高度为20米。 | 已落实 |
项目产生的熔铸铝灰外售综合利用;生活垃圾和污泥由环卫部门集中处置,氧化废水沉淀废渣属于危险废物,应按照《危险废物贮存污染控制标准(2013修正)》(GB18597-2001)的要求建设为先废物暂存库,并严格按照相关规定管理运行。外运处置的危险废物委托具备相应资质的单位运输和处置。 | 严格执行 | 已落实 |
搞好厂区绿化。 | 严格执行 | 已落实 |
进一步落实报告表中提出的各项环保措施,加强各类环保设施的日常维护和管理,确保环保设施正常运行,确保外派污染物长期达标排放。 | 严格执行 | 已落实 |
完善污水处理设施运行管理,特别是含镍、铬污水处理设施的运行管理。制定 | 严格执行 | 已落实 |
严格按照相关规定切实做好危险废物的储存、转移和管理,完善危废申报、暂存、五联单、警示标识等管理制度,确保各类危险废物得到合理转移及处置。 | 严格执行 | 已落实 |
熔铸炉、铝棒加热炉和时效炉燃料全部使用天然气,不得建设燃煤炉窑。 | 严格执行 | 已落实 |
完善突发环境事件应急预案,定期开展突发环境污染事故应急演练,确保在发生污染事故是能及时、准确予以处置,减少污染事故对周围环境的影响。 | 严格执行 | 已落实 |
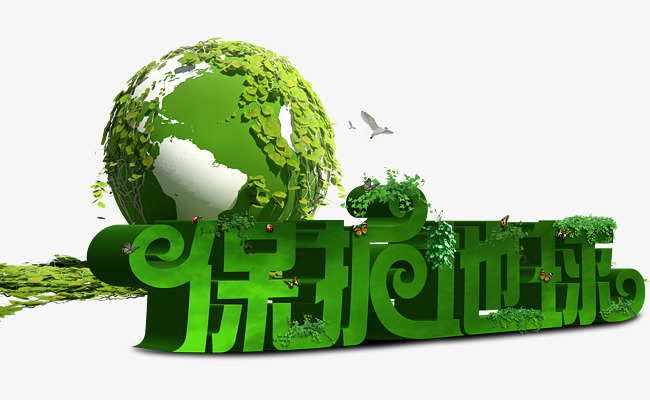
生产工艺固体废物
项目原有熔铸工艺,为响应临朐县环保政策现已淘汰。挤压生产工艺介绍
原料准备
铝棒加热:铝棒运至挤压车间,经过热剪炉加热、裁切成适合后续设备加工的长度,热剪炉以市政天然气为燃料,采取循环热风加热方式,保证加热温度在480~560℃,达到加工温度后方可进行挤压操作。铝棒加热炉每天运行时间约为18h(年运行时间为5400h)。
此过程产生二氧化硫、氮氧化物和烟尘等。
模具预热:根据生产计划选用相应规格模具,送入模具加热炉加热,采取电磁感应加热方式,加热温度在440~460℃,根据机台规格控制模具保温时间,一般保温时间大于2~4小时,但不超过12小时,满足装模温度后方可装模,装模速度应快,根据机台规格应控制在2~5分钟。挤压机模具应定期进行维护修理,修模以人工修整+氮气强化为主。
盛锭筒(挤压筒)预热:盛锭筒应保持清洁干净,并经常清缸,首次开机时采取电加热方式进行预热,加热温度控制在380~400℃,满足加工温度后方可投入生产,正常生产后盛锭筒依靠铸锭自身的余温维持筒内温度,不再需要额外加热措施。
挤压成型
根据生产计划组织挤压生产,首先检查盛锭筒温度、模具温度、铸锭温度是否达到工艺加工要求,全部达到要求时方能装模挤压。根据铸锭、所加工挤压材形状、尺寸、模具工作状态等因素,合理控制挤压速度,确保产出的挤压材光滑平直。采取首件检查方式,检查挤压出的第一支基材尺寸、表面是否符合技术工艺要求,然后将料头切割300mm作为修模依据,另切200mm取样进行外观、尺寸、形状检查,符合技术条件后方可继续生产,否则进行换模、修模处理。
此过程产生下角料、废液压油、废机油等。
风冷淬火
连续产出的挤压型材应合理配制尺寸长度,在适当位置裁断,并通过风机强制冷却淬火,然后传送至冷床上继续利用风机冷却,冷却至50℃以下后,方可进行拉伸矫直处理。
拉伸矫直
冷却后的挤压材经输送带送至拉伸矫直机,首先检查长度、断面尺寸,确保夹头位置和延伸率,其中延伸率一般控制在0.05-2%左右,然后进行拉伸矫直整理,矫直后检查铝材无波浪、弯曲、扭拧等,同时避免出现收口、张开、尺寸负差等现象。
锯切
矫直后的挤压材送至锯切区,首先检查其截面质量、表面质量是否存在缺陷,然后将不合格段切除,再定尺锯切。按照技术工艺要求,控制挤压材的长度公差、切斜度偏差等,防止出现负偏差,完成锯切后修理断面,做到无变形、无毛刺、无油污且整齐美观,然后将合格挤压基材整齐摆放入料筐内,按照同批订单、同种色样、同一型号堆叠,并过磅称重,作好记录后转入下道工序。
锯切过程产生的铝屑。
时效
加工好的挤压基材送入时效炉内消除材料的残余应力,时效炉以市政天然气为燃料,采取热风循环加热方式,温度控制在195~205℃之间,保温时间根据基材形状、壁厚进行控制,测量铝材硬度,达到技术要求后送入检验区检验。时效炉每天运行时间约为12h(年运行时间为3600h)。
此过程产生二氧化硫、氮氧化物和烟尘等。
检验入库
时效后的基材送入检验区,按挤压基材检验规程分别对每料筐基材进行表面质量和机械性能检验,检验合格后按照同批订单、同种色样、同一型号的原则转至指定位置存放,以备后续加工使用。